Introduction
RoadGuard, a cutting-edge road condition monitoring system, offers unparalleled insights into the condition of mining haul road. In this blog post, we delve into the results of a field-validation study, where RoadGuard was installed and tested on a Komatsu 930 haul truck. Join us as we explore the implications of this validation for enhancing safety and efficiency in mining operations.
Field-validation set-up
For this field-validation, RoadGuard was installed in a less than optimal location. Instead of being securely bolted onto a structural part of the frame, it was placed on the floor in the driver cabin behind the driver. Over a duration of 15 hours, we sampled the 6-axis IMU at a frequency of 100 Hz, storing this data at the GPS location where it was measured.
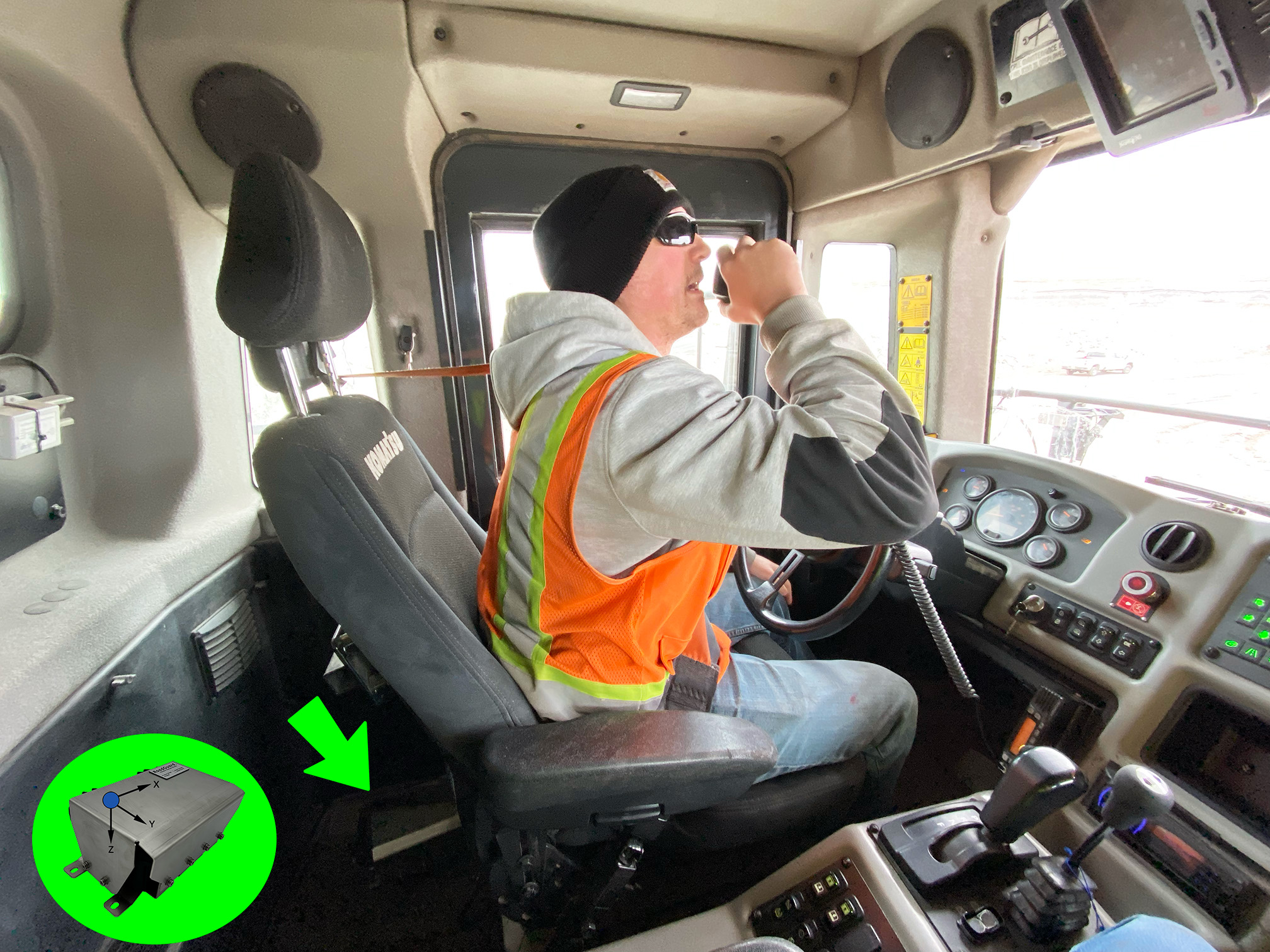
Binning of the data
To analyze the data, we established 5m by 5m GPS bins. All data collected within each GPS bin during the 15-hour recording period were assigned to that bin. Subsequently, the Root Mean Square (RMS) value was calculated for each bin. Low RMS values are represented in blue, while the highest RMS values are depicted in red. Maps were generated for all six axes of the IMU. Below, you’ll find the map for the z-axis of the accelerometer, which corresponds to the direction of gravity.
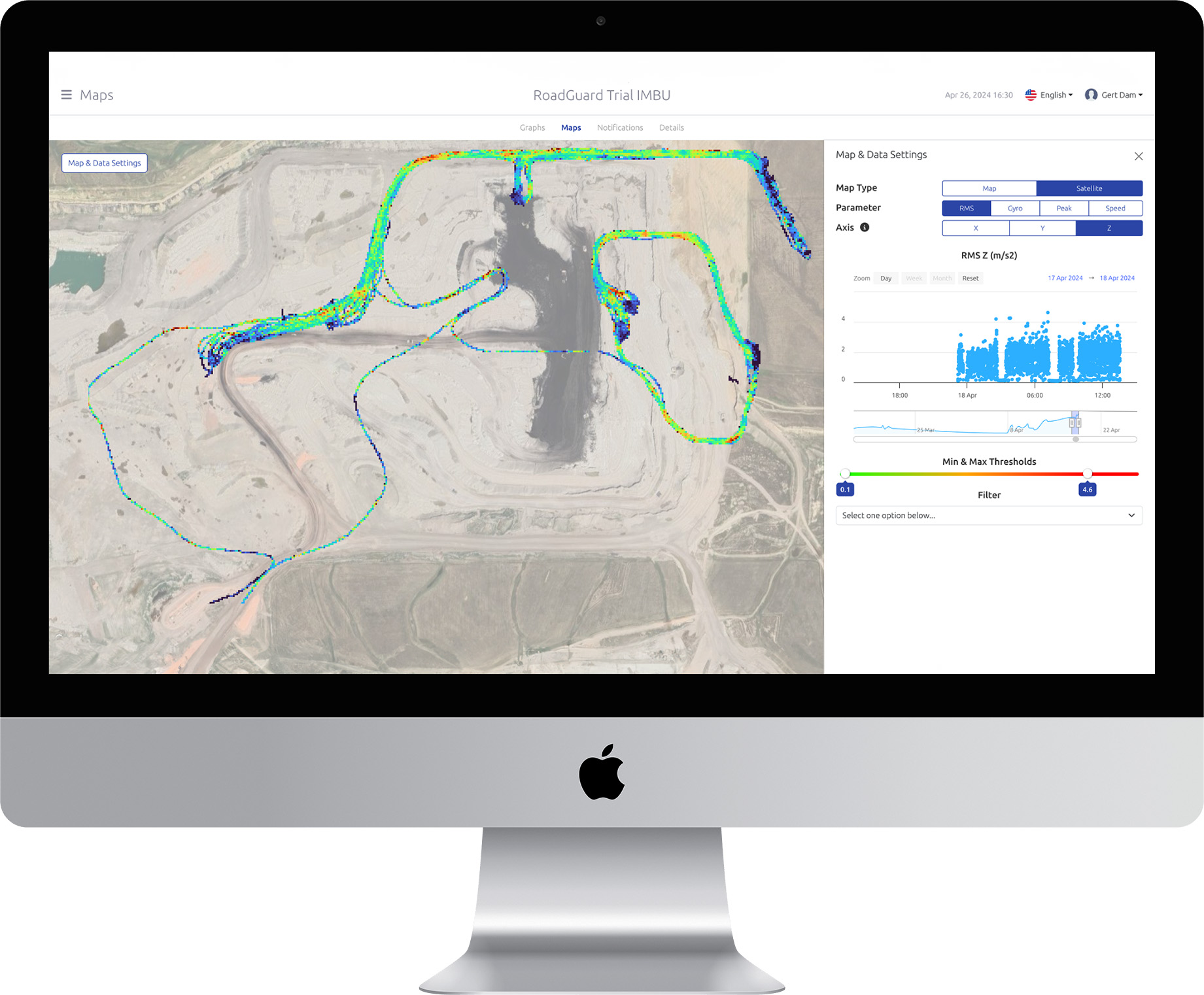
Accelerated wear in bends
Upon examining the generated map, a clear pattern emerges: bends in the road exhibit significantly higher levels of recorded vibrations in the z-direction. This phenomenon is attributed to the increased wear experienced as trucks navigate corners, resulting in side-loading forces acting on the tires against the road surface. The graphics below offer several compelling examples illustrating this observation.
Analyzing Traffic Flow with RoadGuard Data
By visualizing the quantity of samples recorded in each bin, the resulting map effectively highlights the specific areas traversed most frequently by the trucks. This insight proves invaluable for understanding the dynamics of truck movement, particularly around corners and intersections where trucks may frequently pass each other. Analyzing the traffic flow in this manner enables mine operators to anticipate congestion points and predict areas of high wear on the road network. Consequently, informed decisions can be made regarding maintenance schedules and resource allocation, ultimately optimizing traffic flow and prolonging the lifespan of critical road infrastructure within the mine.
As we wrap up our discussion on RoadGuard’s field-validation and its role in mapping road conditions in mines, it’s clear that this technology offers significant benefits for safety and efficiency. Interested in harnessing the power of RoadGuard for your mining operation? Reach out to us today and discover how RoadGuard can revolutionize your road condition monitoring strategies.